Case Studies
Meet the Manager: Thomas, Tate & Lyle Sugars
Meet the Manager: Thomas, Tate & Lyle Sugars working with CQM on Continuous Improvement
Setting the scene
My name is Thomas Sutton, I am the Continuous Improvement Manager for Tate & Lyle Sugars, part of ASR Group, and we produce food and beverage ingredients for a global market. We have recently completed an Improving Operational Performance level 2 cohort with CQM Training & Consultancy, below is an overview of how we have found this process.
How have you found working with CQM?
We have found our time working with CQM to be very rewarding. Our group of learners have had to face the challenges presented throughout the pandemic, but CQM have supported us through this tough time and were accommodating throughout, such as quickly adapting with remote training sessions. We have had Conor Horgan as our tutor and he has been brilliant to work with.
Why Continuous Improvement?
We believe in making continuous improvement training as widely available to as many people as possible, in addition to supporting the requirements of our new packing team structure. We recognised the need to build a large number of individuals that have Continuous Improvement understanding across our operator group. We believe this in turn will help us realise a significant impact on our operations with a sustainable approach to problem solving and waste elimination.
Throughout the pandemic we also noticed a slight increase in staff turnover within the operator group, this reinforced the need for development and training, not only for the culture change of the continuous improvement ideas within the group, but also to improve employee retention.
What key impact / improvement have you noticed from the programme?
Carrying on with the idea of a change of culture, we have really noticed this developing amongst our apprentices as well as proactive self-improvement for individuals in the operator group. Now we have that tangible qualification to support the new team structure within our packing department we have also noticed that continuous improvement is mentioned and discussed frequently, so it’s great to notice that it is being understood outside the boundaries of just the management group, hopefully this will continue to grow.
The apprenticeship has allowed not only benefits in savings for the business but huge personal benefits for the individuals. 90% of the first cohort have progressed into more advanced roles within the business, some of these during the apprenticeship and some after. As I mentioned earlier this also helps with staff retention. It has also helped us lay the groundwork for the 5S drive we’re going through in 2022 in operations, and we are using the apprentices as cell leaders within this.
How do you make apprenticeships an affordable and viable route?
The apprentice levy is a real revelation, giving us an affordable route to CI training. It has sometimes been a little restrictive in the requirements for attendance and time contribution from the group, but this was exacerbated by the labour pressures of the pandemic. I was sceptical about some the early compulsory material around British values and Health and Safety, but it actually really complements some of the wider cohesiveness we are aiming for as a company.
What’s next?
Since the completion of the Improving Operational Performance apprenticeship, we are pleased to say that Tate and Lyle are moving forward with another cohort. Although we no longer were offered the IOP course they made the move across to the Lean Manufacturing Operative Level 2 qualification.
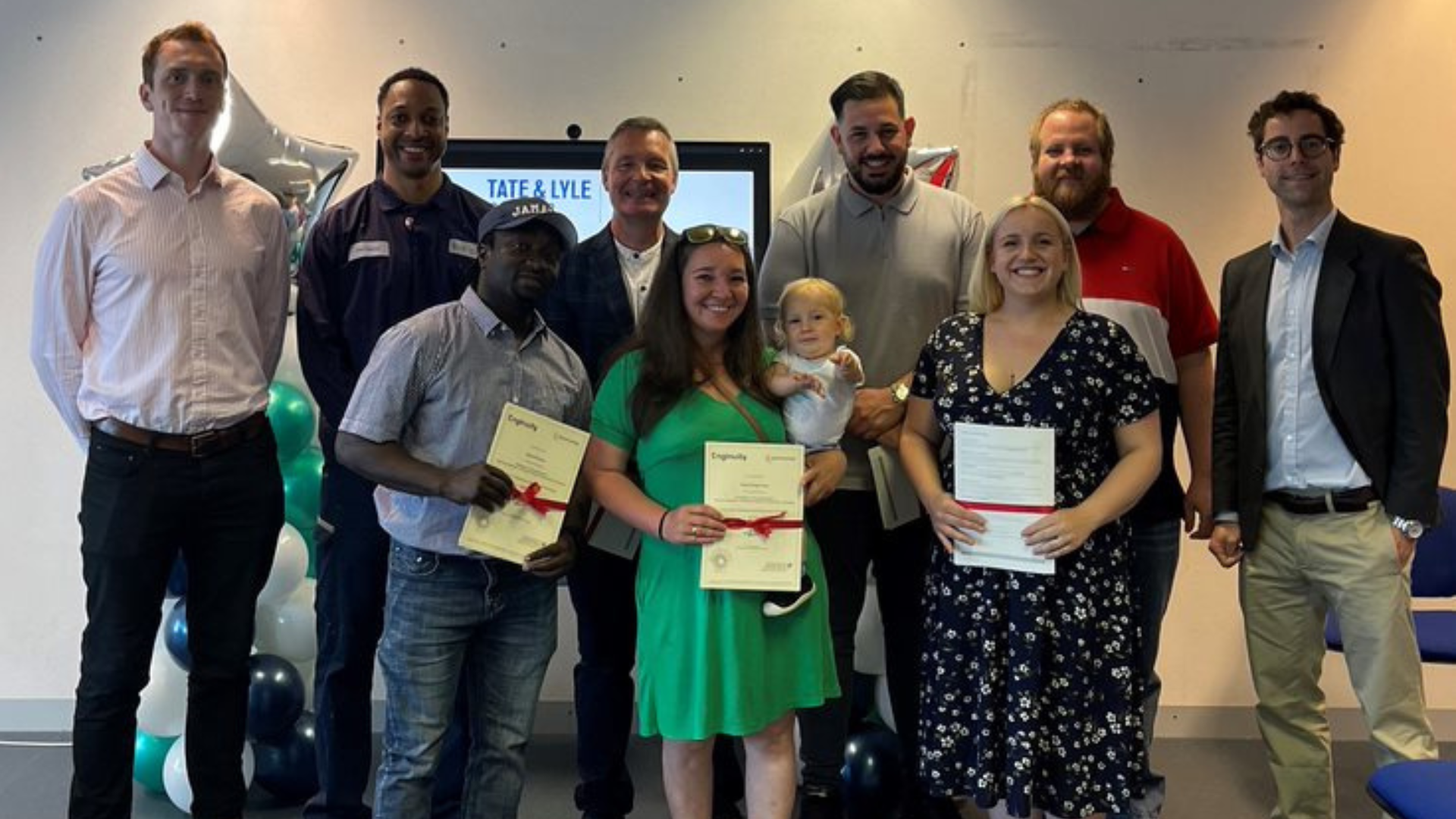
All of us at CQM Training & Consultancy are pleased to see the fantastic results of this Improving Operational Performance Level 2 cohort with Tate & Lyle and look forward to continuing working together on the new Lean Manufacturing Operative apprenticeship programme.
If you’d like to find out more about our Lean Manufacturing Operative apprenticeship please click the button below or contact us.