Articles
Tariffs, Tensions & Talent: Why the Real Response to Global Trade Shocks Starts with People
Tariffs, Tensions & Talent: Why the Real Response to Global Trade Shocks Starts with People
As UK manufacturers come to terms with a sudden spike in U.S. tariffs – part of a broader shift toward economic nationalism and de-globalisation – they face a stark choice: react defensively or adapt boldly.
While the short-term impacts of these tariffs will sting, especially in automotive and steel, they also offer a strategic window of opportunity. Unlike many EU countries hit with even steeper U.S. tariffs, UK manufacturers have a comparative edge. But to fully capitalise on this, the focus can’t just be on the export data. It needs to be on people.
Turning a Challenge into Competitive Advantage
Tariffs often dominate headlines, but behind every trade policy is a deeper truth: the most resilient economies are those that can deliver more value at lower cost – without compromising on quality or sustainability.
That’s where UK manufacturing can thrive. With smaller tariffs than some competitors, there’s an opportunity to undercut rivals while still maintaining premium standards. But that advantage is only sustainable if manufacturers confront two critical issues:
- The growing skills gap across technical and leadership roles.
- The need for leaner, smarter, more sustainable operations.
Lean Thinking + Smaller Tariffs = Double Advantage
The solution lies in embracing Lean, Continuous Improvement, and AI-ready upskilling – not as buzzwords, but as a structured, measurable approach to performance.
Take Lean Six Sigma, for example. At its core, it’s about eliminating waste, streamlining processes, and driving cost savings, which directly offsets the increased costs from tariffs, inflation, or supply chain disruption. More importantly, it empowers teams at all levels to sustain improvements over time.
Now, layer that onto the current global context:
- UK firms already benefit from lower tariffs than EU competitors.
- Efficiency gains through Lean mean UK products become even more cost competitive.
- Quality-focused, sustainable British manufacturing has growing appeal in global markets.
Combined with reshoring that is on the rise, reducing process inefficiencies becomes essential.
Together, this creates a “double advantage”: operational agility combined with a pricing edge.
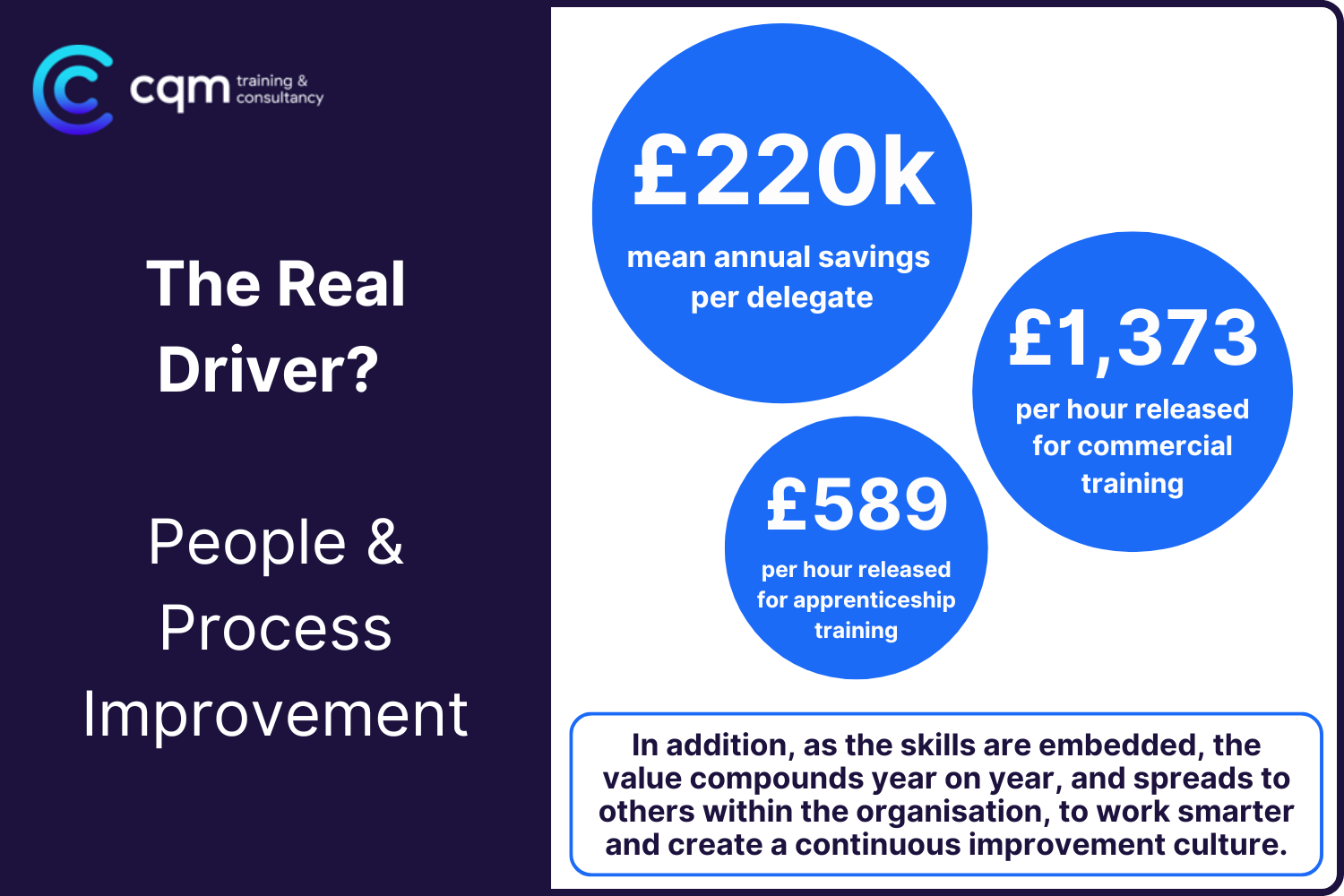
The Real Driver? People & Process Improvement
Despite the noise around AI, robotics, and automation, one thing remains clear: none of it works without human capability.
According to recent Make UK research, manufacturers overwhelmingly see investment in skills as central to digital transformation and long-term growth. But the gap between intent and action is still wide – especially in embedding continuous improvement practices.
That’s where organisations like CQM Training & Consultancy are playing a vital role.
“The world is changing. Politicians are challenging the decades-long globalisation consensus. Economic nationalism is rising up the agenda. Improving within-country productivity has become more important than ever.
At CQM, we don’t do pure consultancy, we work to improve the skills within the workplace which then drive productivity in the medium and long term. All of our programmes, whether in Continuous Improvement, Food Innovation or Management Development have at their core process improvement that delivers organisational benefit, usually mapped to cost savings”
Managing Director of CQM Training & Consultancy, Andy Cheshire.
The numbers speak for themselves. From analysing outcomes across CQM learners who have delivered work-based projects as part of their programmes, signed off by their employers:
- The mean annual savings per delegate exceeded £220,000.
- That equates to £589 per hour of release for apprenticeship learners.
- That equates to £1,373 per hour for commercial training clients.
- In addition, as the skills are embedded, the value compounds year on year, and spreads to others within the organisation, to work smarter and create a continuous improvement culture.
The Sustainability Payoff
It’s not just about the bottom line, although this is a huge part of staying competitive. Lean and CI methodologies also support sustainability by:
• Reducing material and energy waste.
• Creating shorter, more localised supply chains.
• Embedding ESG principles into daily operations.
For example, taking a look at one standout project on one of CQM’s Lean Six Sigma Green Belt courses was led by Louise Rewcastle-Adams, Carlsberg Britvic’s then Customer Operations Manager, since promoted to Category Demand Planning Manager following the course .
Louise’s project tackled inefficiencies with a major supermarket chain whose systems weren’t aligned with Britvic’s production sites. This misalignment caused excessive and avoidable internal stock moves, resulting in substantial cost, labour and environmental implications.
By implementing a more systemised approach to order creation, Louise’s project reduced unnecessary stock moves and manual intervention, creating availability for additional sales.
“Through the project, we increased our vehicle utilisation, reduced CO2 emissions and slashed the average miles travelled per pallet substantially. The annual savings came to just under £1m, but what really sold the changes to the customer was the sustainability aspect. They quickly bought into the idea because we had all the data and insights to show it was the right thing to do. This course has not only enhanced Carlsberg Britvic’s credibility with customers but also strengthened our internal supply network. It proves that the right tools and training can unlock dramatic improvements.”
Skills development, therefore, is not a “nice to have” – it is a core pillar of economic, environmental, and operational resilience. You can learn more about the impact of Lean Six Sigma Green Belt training in our latest case study with Carlsberg Britvic.
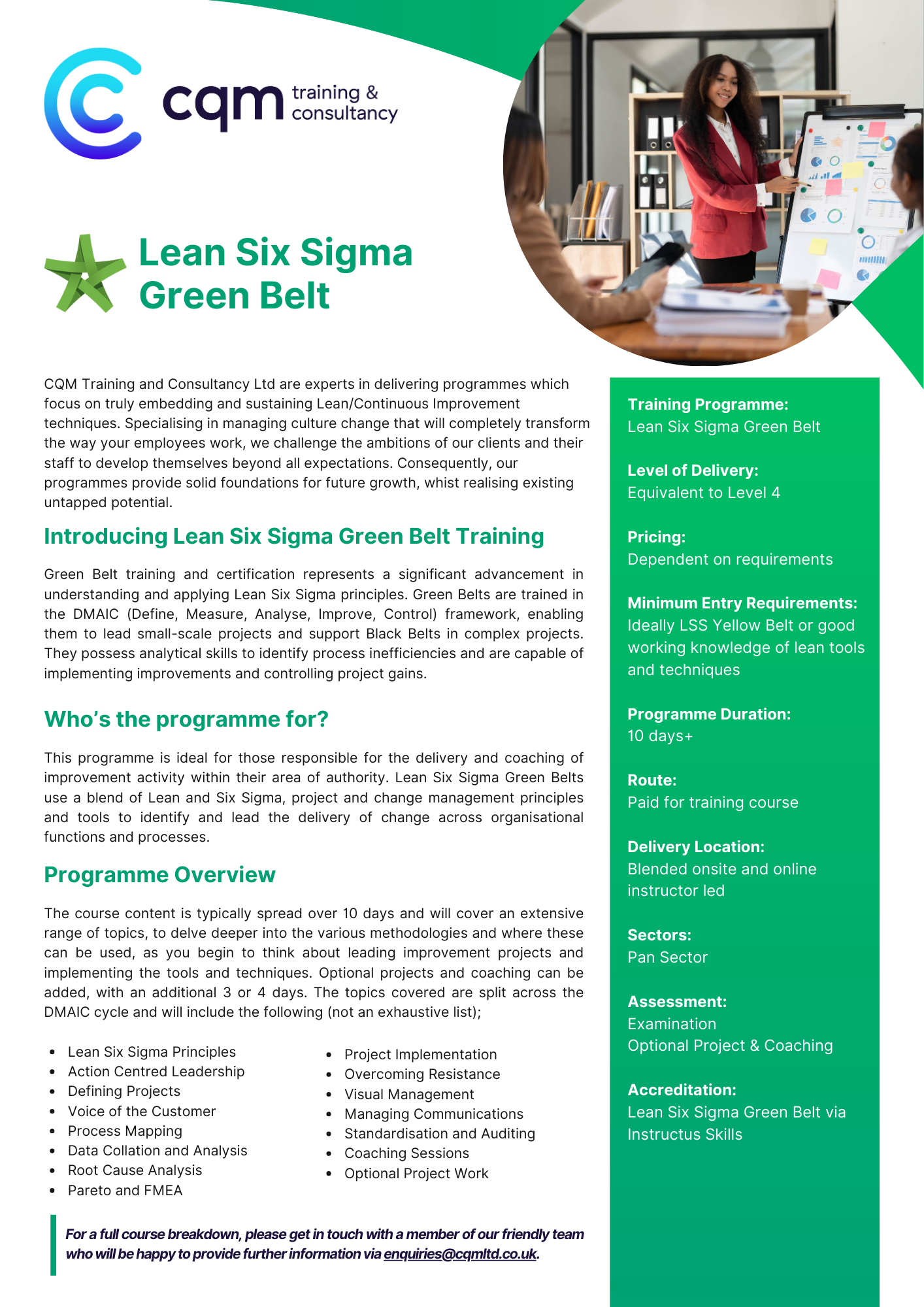
A Call to Action
If UK manufacturing is to thrive in a more protectionist world, investing in technology must be matched with investment in people. Tariffs may come and go, but the skills we build today determine whether we survive the next disruption or lead through it.
As CQM’s MD puts it, “Governments, in partnership with industry, can’t afford not to continue investment in the skills agenda. The return on investment is unbeatable.”
UK manufacturers have a choice – be reactive or become resilient. With smaller tariffs, a powerful heritage in quality, and a workforce equipped through Lean and Continuous Improvement, there’s every reason to bet on Britain.