Articles
What is Lean Six Sigma and Why is it Important?
What is Lean Six Sigma and why is it important?
In today’s competitive business landscape, organisations are striving ever more to improve their processes, quality, sustainability and value, reduce waste, and enhance overall efficiency. The aim for many organisations is to boost their bottom line and build their competitive advantage.
By combining Lean and Six Sigma, this provides a strong methodical approach and toolkit for improving processes and wider operations. Below, we will delve into what is Lean Six Sigma and why it is critically important for organisational success.
What is Lean Six Sigma?
Lean Six Sigma combines Lean principles and Six Sigma practices to improve efficiency by reducing waste and defects. We look at each separately, before exploring how together they can provide a structured approach to problem solving, project management and continuous improvement.
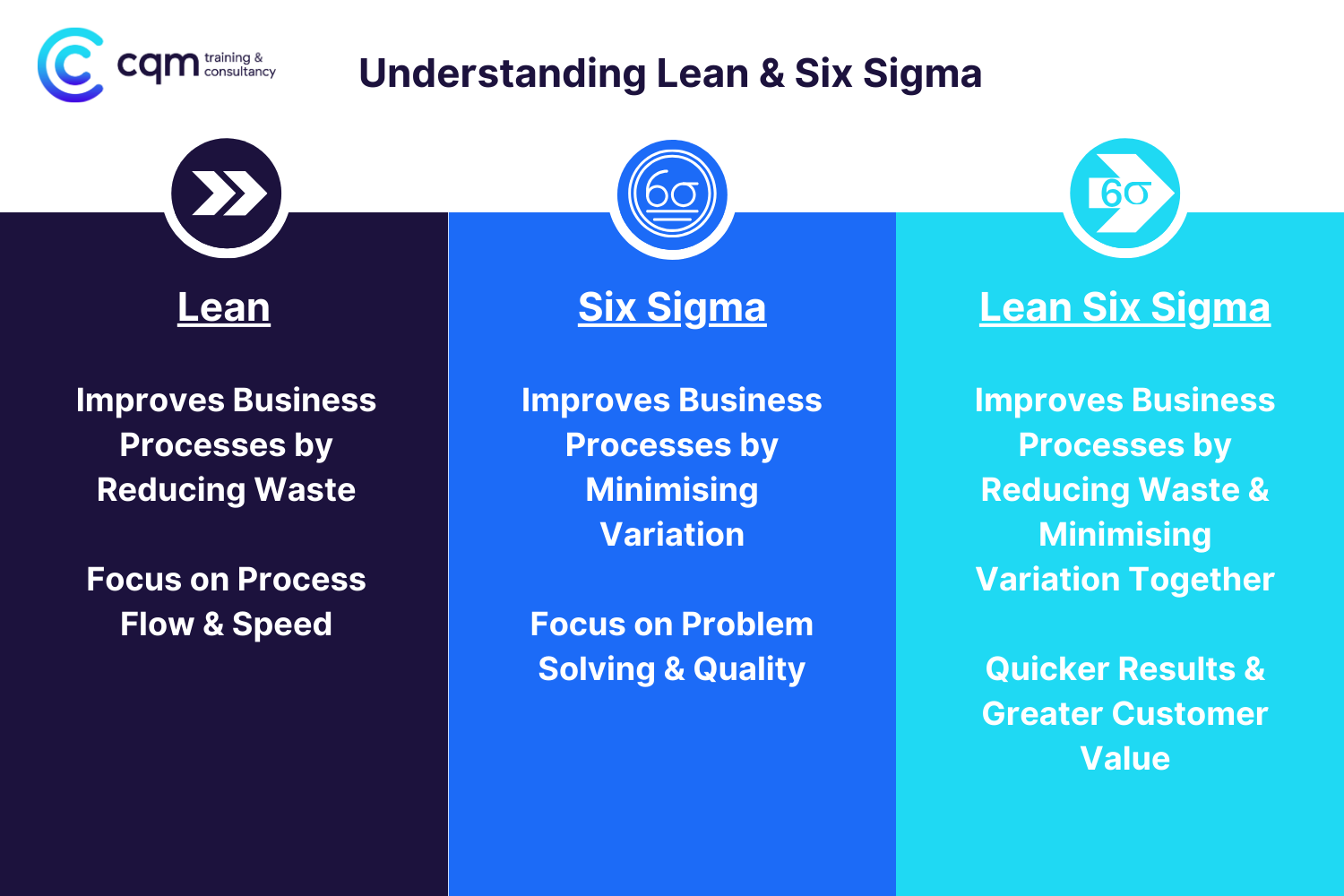
Lean
Lean methodology, also known as “Lean,” is a systematic approach to optimising process flow and reducing waste. It originated from the lean manufacturing and production industries, initially developed by Toyota in the 1950s. Because of its universal application, a wide range of sectors have implemented Lean.
Lean focuses on finding and removing activities that don’t add value, using a variety of lean improvement tools like the 8 wastes of Lean (common acronyms DOWNTIME or TIMWOODS), Kaizen, 5S, Value Stream Mapping and so on.
By adopting lean thinking, organisations can streamline their processes, reduce costs, and enhance customer value. You can learn more about the five key lean principles here.
Six Sigma
Six Sigma is a data-driven approach focused on reducing defects and variations in processes. It aims to achieve near-perfect quality by identifying and addressing root causes of problems. It relies on data analysis and statistical methods to make informed decisions.
The term “Six Sigma” refers to a statistical concept where a process operates within six standard deviations from the mean. In practice, achieving Six Sigma levels of performance means that the process will produce only 3.4 defects per million opportunities. Imagine that.
Six sigma focuses on reducing these variances and defects, to deliver better consistency and quality, using a variety of statistical related tools like Critical to Quality (CTQ), Defects per Million Opportunities (DPMO), Failure Mode Effects Analysis (FMEA), Pareto charts and so on.
Lean Six Sigma
When combined, Lean Six Sigma creates a comprehensive approach to process improvement that addresses both efficiency (Lean) and effectiveness (Six Sigma). Lean Six Sigma typically utilises the DMAIC framework to enhance existing processes and the DMADV framework to create new processes.
DMAIC (Define, Measure, Analyse, Improve, Control) is a framework for existing process improvement. DMADV (Define, Measure, Analyse, Design, Verify) is a framework for designing new processes. Within each stage there are a variety of tools and techniques to support successful project outcomes and process improvements.
You can get a good introduction to lean and the basic tools through our essential lean awareness programme. You can find out more here.
Importance of Lean Six Sigma
Embracing lean six sigma is hugely important in achieving organisational growth and success. Here are the benefits of Lean Six Sigma:
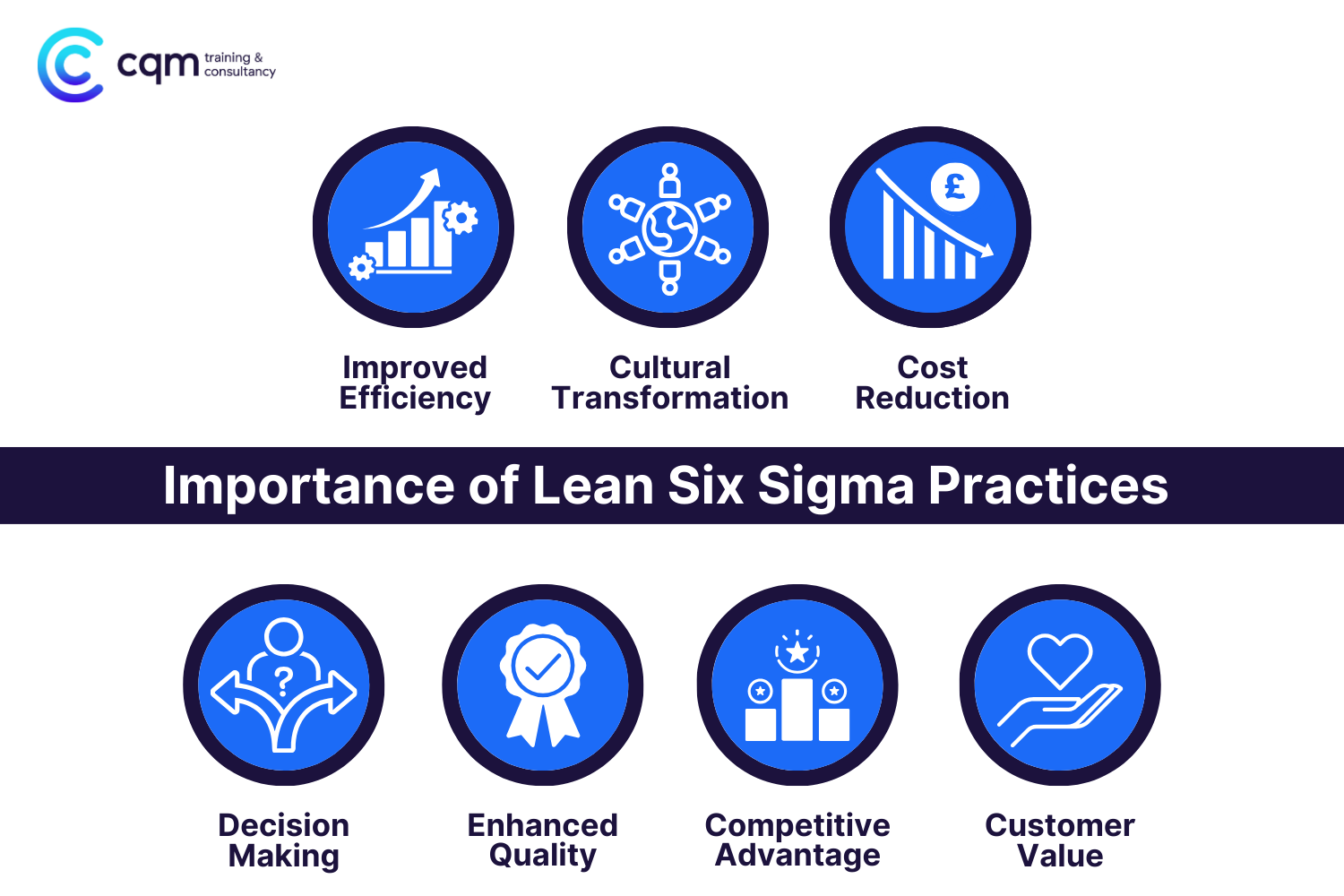
- Improved Efficiency. By reducing waste and streamlining processes, organisations can achieve higher productivity, reduced lead times, and increased throughput.
- Enhanced Quality. With greater emphasis on reducing defects and variations, this leads to higher product and service quality, resulting in greater customer satisfaction.
- Cost Reduction. Focussing on this supports reduction of time, effort and waste which directly translates to cost savings.
- Informed Decision Making. Embracing data-driven insights enables stakeholders to make informed decisions based on objective evidence rather than assumptions.
- Cultural Transformations. Encourage employees at all levels to consistently improve, innovate, collaborate. This fosters a cultural shift towards continuous improvement.
- Competitive Advantage. Harness a competitive edge by delivering higher quality products or services faster and at a lower cost than competitors. With sustainability high on the agenda for many organisations, securing competitive advantage is crucial.
- Customer Centric Approach. Showcase understanding and meet customer needs. This leads to products/services that align more closely with expectations, creating greater value.
Conclusion
Lean Six Sigma is not just a methodology. It’s a proven approach that empowers organisations to achieve greater success.
By integrating Lean’s waste reduction principles with Six Sigma’s data-driven problem-solving techniques, businesses can drive efficiency, quality, customer value and innovation. Using Lean Six Sigma can benefit any organisation, regardless of industry, despite being deeply rooted within the manufacturing sector.
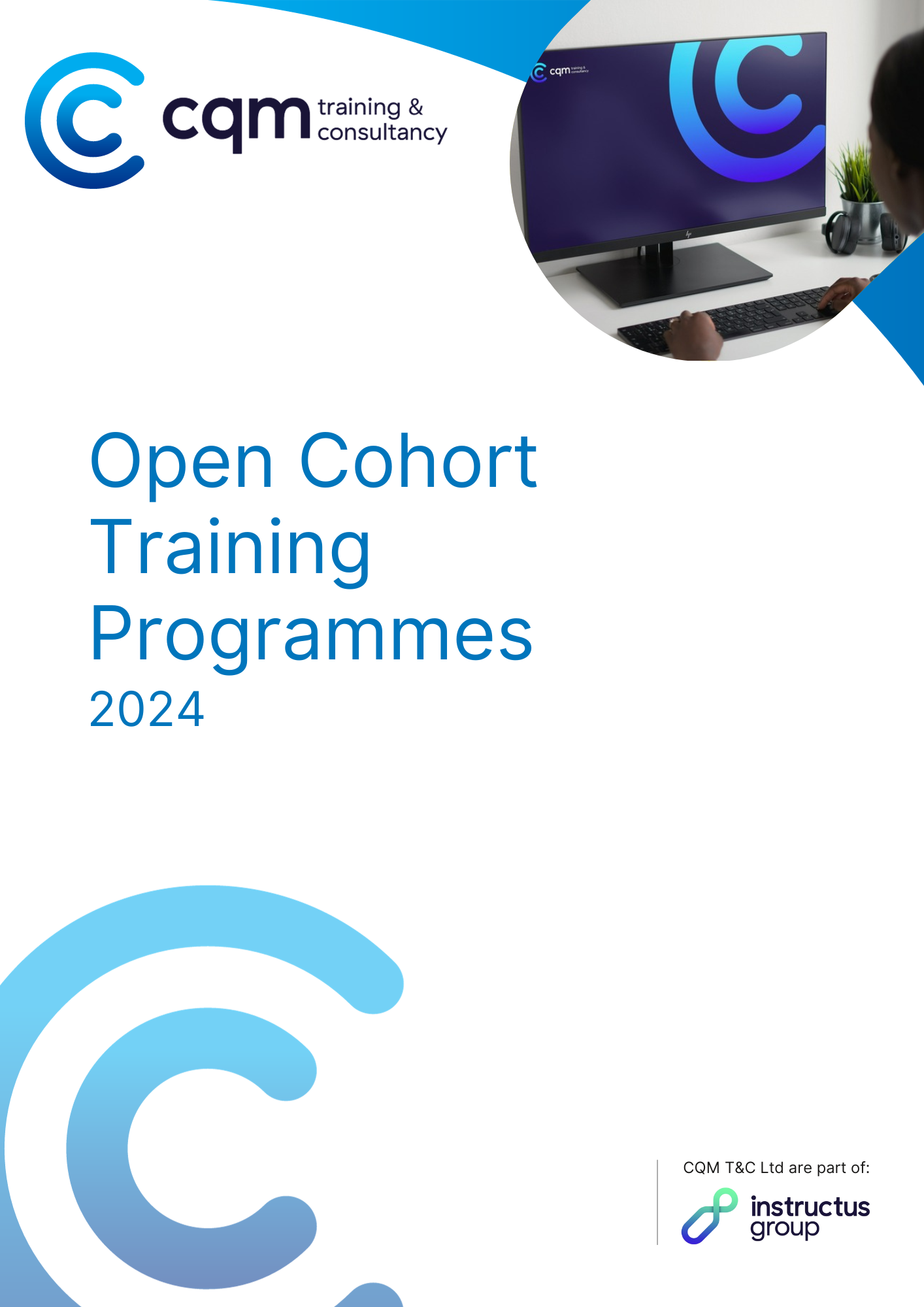
Have you thought how Lean Six Sigma can benefit you and your organisation?
It is likely your organisation has adopted some Lean or Six Sigma approaches within their practices, but there is always room for improvement. Whether your organisation truly embraces Lean Six Sigma, or is looking to begin their journey towards operational excellence, investing in the right people with effective training is so important to ensuring that the key benefits are realised to maximum potential.
CQM Training & Consultancy are specialists in Lean Six Sigma training with programmes available via our funded improvement apprenticeships or shorter lean six sigma belt training programmes (white belt, yellow belt, green belt, black belt and master black belt).
We understand that there is lots of lean six sigma/CI training available on the market, so we have put together a simple 5 step guide to support you choose the right training provider. It is important you consider what you want to get from the programme and ensure it is value for money with the returns you anticipate.