Articles
Addressing Barriers to Manufacturing Growth in 2025
Introduction: Addressing Barriers to Growth in UK Manufacturers in 2025
A report released late last month highlighted the extent of the skills shortage threatening the growth and competitiveness of the UK’s manufacturing sector.
Produced by The Manufacturer in collaboration with Barclays Corporate Banking, the “Now hiring: understanding and tackling the skills shortage in UK manufacturing report” presents a detailed analysis of the barriers manufacturers face and the innovative strategies being deployed to address these challenges.
One of the key areas we picked out from a training provider perspective was that 75% of manufacturers identify skills shortages as their biggest barrier to growth, followed by recruitment challenges (36%) and talent retention (32%) which are all people related. As a result, 91% of manufacturers are taking on more responsibility to train their workforces, using this as a strategy to attract, develop and retain key skills and talent.

So how are manufacturers looking to train their workforces?
Internal training and skills assessments
Several manufacturers have well-structured internal programmes, often managed by dedicated teams or academies, and use skills assessments to identify gaps and needs. While this is a great approach, and something we have worked closely with the likes of Johnson Matthey on, who recently won the Princess Royal Training Award 2024 as a result, it is important to implement this as part of a wider strategy to recruit and retain key talent.
This can also be supported by “Train the Trainer” courses, to ensure any internal training is provided both efficiently and effectively.
Apprenticeships
Apprenticeship schemes came out as the number one initiative to recruit skilled labour, cited by 74% of respondents, but doesn’t appear as a commonly thought way to retain.
Manufacturers expressed mixed sentiments when it came to the Apprenticeship Levy and the value it represented. A significant proportion (43%) of manufacturing organisations said they currently do not use the Apprenticeship Levy. And while 57% of manufacturers said they do use the Apprenticeship Levy, only 36% said it is worthwhile and represents good value for money.
On top of this, currently, there are apprenticeships critical to supporting manufacturers under review such as the Improvement Technician Yellow Belt Level 3 and Improvement Specialist Level 5 which may well not continue as we look ahead to 2025. So, what’s the alternative to still get access to work based learning, critical knowledge, skills and behaviours?
Accredited commercial training
While internal efforts are significant, many organisations also rely on external training for more specialised areas and when it comes to what manufacturing businesses are doing to address people/ skills shortages, reskilling was the top tactic, as cited by 75% of survey respondents. Shop floor efficiency and greater use of automation, including AI, were the second and third most prevalent tactics, cited by 62% and 49% of respondents respectively.
With this in mind, investing in continuous improvement as an example, particularly through Lean Six Sigma Black Belt training, is a critical strategy for manufacturers to address skills shortages, recruitment challenges, and talent retention while driving long-term growth and profitability through all of these top 3 areas. Here’s how Lean Six Sigma Black Belt supports reskilling, efficiency and adopting new technologies:

1. Addressing Skills Shortages
Lean Six Sigma Black Belt training equips employees with advanced problem-solving and process optimisation skills. By upskilling existing staff, manufacturers can fill critical skill gaps internally, reducing reliance on external recruitment in a tight labour market. This builds a more resilient workforce capable of meeting operational challenges.
2. Boost Bottom Line
Empowering key employees Lean Six Sigma Black Belt training and accreditation will provide them with the toolkit and influence to create process improvements and facilitate change. With a work based project(s) and coaching to guide them, this knowledge can be embedded, generating a measurable return on investment and the potential for significant cost savings that impact the bottom line.
3. Improving Recruitment and Retention
Employees trained in Lean Six Sigma often feel more valued and empowered, as they see tangible investment in their development. Offering advanced training like Black Belt certifications enhances the company’s reputation as an employer of choice, making it easier to attract top talent. Furthermore, employees who see clear paths for career progression (consistent with 49% manufacturers believe providing clear personal development plans and progression routes) are more likely to remain with the company, reducing turnover costs.
4. Driving Process Efficiency
Lean Six Sigma Black Belts lead initiatives that streamline processes, reduce waste, and improve quality, directly contributing to higher productivity and cost savings. In a competitive manufacturing landscape, these improvements are vital to maintaining profitability and ensuring customer satisfaction. This training can be filtered down, right through to the shop floor, creating a ripple effect of efficiencies and pro-active problem solving.
5. Enabling Innovation
Continuous improvement methodologies empower teams to innovate by analysing and solving complex operational issues. Black Belt-trained professionals often spearhead efforts to adopt new technologies such as AI automation, enhance product offerings, and optimise supply chains, positioning manufacturers for sustained growth over the longer term.
6. Creating a Culture of Excellence
Investing in Lean Six Sigma promotes a culture of accountability and data-driven decision-making. This cultural shift not only boosts operational performance but also engages employees, building a sense of ownership and collaboration across the organisation.
7. Ensuring Scalability and Adaptability
Lean Six Sigma Black Belts have the skills to scale improvement efforts across multiple departments and locations. This adaptability ensures that the business can respond effectively to market demands, regulatory changes, and global competition.
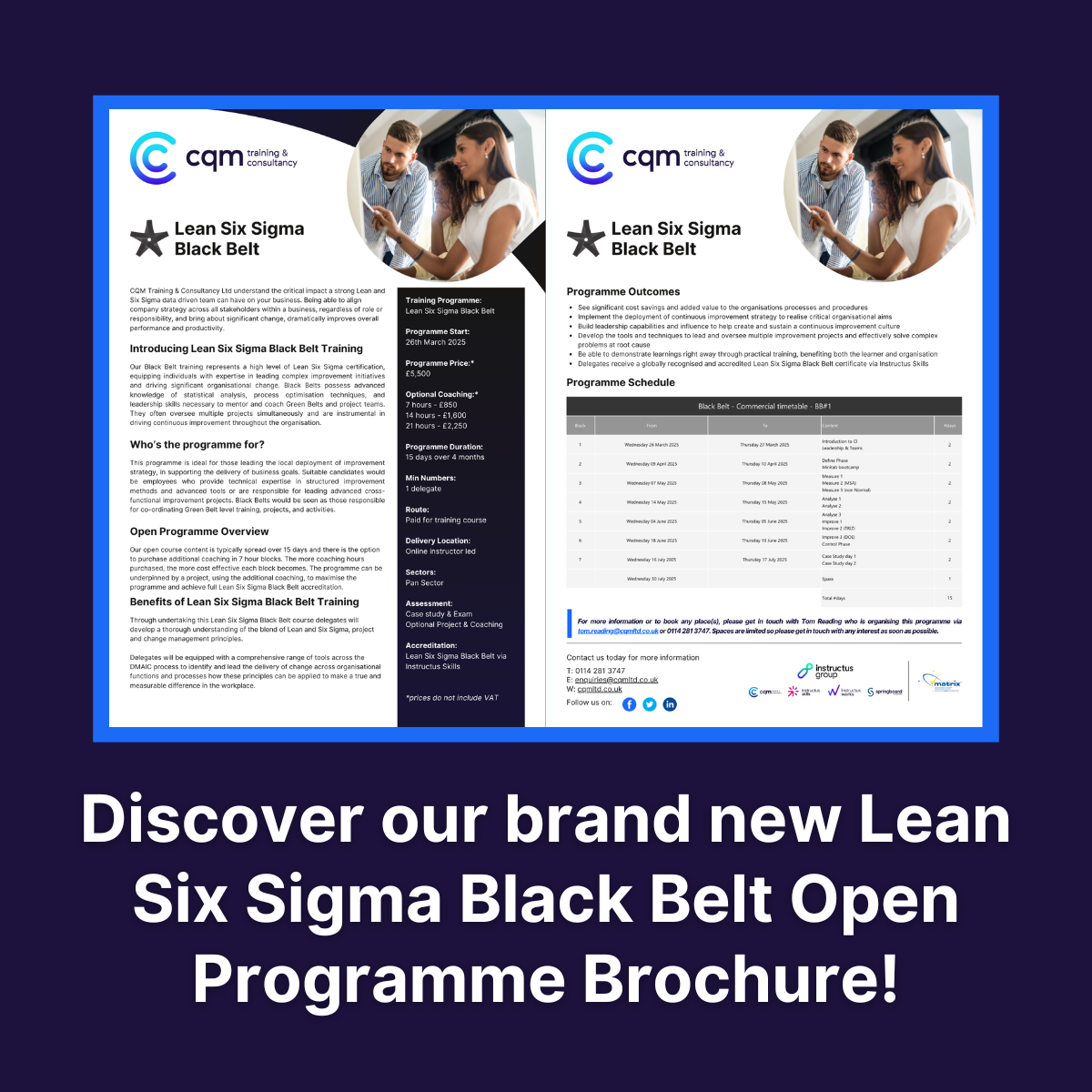
Discover More Benefits
By focusing on Lean Six Sigma Black Belt training as an example, manufacturers not only mitigate immediate challenges with skills shortages but also lay the foundation for sustainable growth, enhanced profitability, and a competitive edge in the market.
You can discover more about our Lean Six Sigma Black Belt training programmes at our brand-new and completely free discovery event taking place on Thursday 19th December via MS Teams (14:00 to 15:00 GMT).
Summary – Driving Manufacturing Growth
Deciding on the right training can be difficult, and it should never be a tick box exercise. Training represents an investment in people, skills and organisational capability, and as such should be aligned with the goals of the business. Effective training supports attracting and retaining talent and skills, creating bottom line cost savings, and future proofing your operations. Ineffective training is forgotten, unappreciated and drives no value.
Look out for our upcoming thought leadership article on the Value of Training, that aims to simplify what training should be, and how you can approach effective training solutions that deliver results. In the meantime, feel free to get in touch with our friendly team to see how we can support your manufacturing organisation.